Can Analog Quality Match Digital? Discover How
When a vinyl record is played the sound waves are captured in grooves etched into the record. Then these waveforms are converted to electrical signals that are reproduced on speakers for us to listen to. When we convert an analog signal to digital it has to be sampled at specific intervals – like blocks on
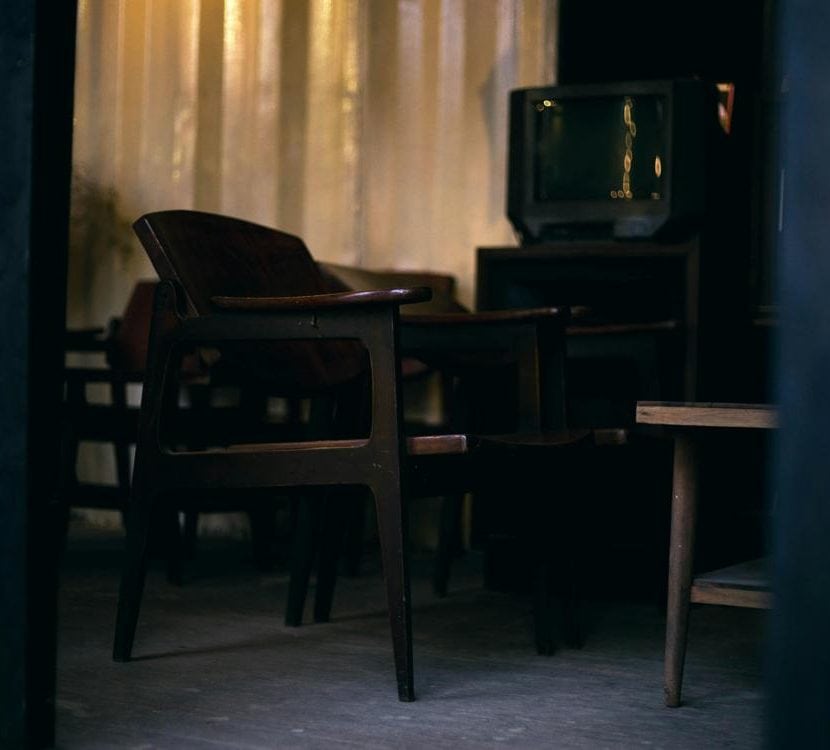
When a vinyl record is played the sound waves are captured in grooves etched into the record. Then these waveforms are converted to electrical signals that are reproduced on speakers for us to listen to.
When we convert an analog signal to digital it has to be sampled at specific intervals – like blocks on graph paper. This creates a loss in quality.
Defining Analog
The word analog is often used to describe old technology like vinyl records and clocks with hands. However, the meaning of analog has a wider context in technology and science. In this sense, it refers to systems that use measurable quantities, like a physical wave that can be changed up or down. This is contrasted with digital which uses signals that are on or off and function in binary code.
Analog devices can record, reproduce, transmit or broadcast information that is continuous or has a virtually infinite number of grades of transparency, temperature, voltage, resistance, rotation, or pressure. This information is encoded on an analog medium, such as photographic film or acoustic waves in a microphone. An analog signal can be described as a physical wave that changes up or down in amplitude. This change can also be smooth or not smooth.
An analog signal can be represented as a curve with its high point at the peak of the curve and its low point being just below the bottom of the curve. The curve can have many shapes, but the most common one is a sine wave or a bell-shaped curve. An analog device can capture this wave and turn it into fluctuating electronic pulses to represent data. The pulses can then be converted to a digital representation of the original information.
This process of analog to digital conversion is known as sampling. The most popular sampling rate is 44.1kHz, but it is possible to go higher or lower depending on the design of the analog to digital converter. The higher the sampling rate, the better the resolution of the converted signal. This is because a higher sampling rate results in more precise conversion of the analog signal to a digital value.
An advantage of the analog to digital conversion is that it can remove noise that may be present in the original signal. This can be caused by vibration in the recording system, electronic noise from the analog to digital converter and other sources. The downside is that it can also introduce noise from the digitization process. This can be the result of either overshooting or undershooting the original analog signal, which is then sampled at a resolution that is too high or too low.
Analog to Digital Conversion
An analog signal is converted to digital form by an analog to digital converter (ADC). The ADC converts the continuously varying analog signals into a series of discrete digital values. This process is also known as sampling. The accuracy of the digital values created by an ADC depends on two factors: quantization level and sampling rate.
When an ADC digitizes an analog signal, it samples the original analog input signal at each falling or rising edge of the sample clock. Each sample is then changed to a 0 or 1 according to its location in the original analog signal. The number of samples used is called the bit rate and determines the resolution of the resulting digitized output.
The ADC converts the sampled data to a digital signal by using a successive approximation algorithm. The ADC outputs the resulting digital value in a series of binary bits.
An ADC can be designed to have different bit lengths, and the more bits it has, the higher the resolution of the resulting digital output. However, the cost and power consumption of an ADC increases with the number of bits it uses.
To achieve high-resolution digitized output, an ADC requires that each bit is very accurate. To ensure that each digital value represents the correct data, the ADC may use a technique called dithering. Dithering reduces the effects of quantization distortion by converting some of the digital bits to noise.
An ADC is a key component in many electronic devices that convert continuous physical quantities into digital form. For example, air conditioners utilize sensors to detect temperature that are then converted by an ADC to a digital signal to control the unit. Similarly, medical devices like MRI machines and X-Ray equipment transform analog physical quantities into digital signals for processing. Mobile phones also rely on an ADC for converting the analog voice signal into digital before transmission. Even computer systems rely on an ADC to turn the analog electrical signals into a digital representation of the program code being executed. In order to understand how the ADC works, we can break the circuit down into four different blocks as shown in Fig 12.3. The block diagram of an analog-to-digital converter can be seen in Fig 12.4.
Analog to Digital Converters
Analog to Digital converters are electronic integrated circuits that convert analog inputs such as voltages to binary data which is a sequence of ones and zeroes. These are essential devices for converting data from sensors such as photoresistor or thermistor into a form that microprocessors and computers can understand.
Computers “think” in terms of binary digital data and must convert analog signals into this format before they can process the information. For example, a telephone modem uses an ADC to convert the incoming analog audio data on a twisted pair line into digital data that can be processed by a computer microprocessor.
To achieve this conversion, an ADC compares a sample of the analog signal (produced by using a Sample and Hold circuit) to a reference voltage. The ADC converts this comparison into a binary code and outputs this as a binary number. The two factors that determine the accuracy of this converted data are the sampling rate and the bit resolution.
The higher the sampling rate, the more accurately the ADC can convert the analog signal, much like how one would convert old tapes. However, the ADC must be able to keep up with this sampling rate to avoid missing portions of the original analog signal which is called aliasing. If the ADC is not able to keep up with this requirement it will be unable to reproduce the original analog signal which would result in a system error.
A number of different methodologies can be used to accomplish the analog to digital conversion. The most common approach is called successive approximation. This technique samples the analog signal each cycle of the clock and then compares this sample to the previous one. Each sample is a bit and the bits are compared to determine if they correspond to either a zero or a one. Each bit represents a voltage interval of the analog signal and is therefore a very accurate representation of the original analog signal.
The other method of converting analog to digital is integrating. This is an alternative to successive approximation and utilizes a different logic structure. This type of ADC is often referred to as an 8-bit ADC because it can represent an analog signal with up to eight different bits of resolution. This is an important feature because it allows the ADC to be used in applications where precision is more critical than speed.
Analog to Digital Converter Reviews
An analog to digital converter (ADC) converts an analog signal into a series of binary numbers. Each bit represents one of the 256 possible code transitions that can occur in a digital signal. In the ideal case, a change in a digital bit will correspond to exactly 1 LSB of an analog signal. Differential linearity error is the deviation between these two values. Analog to digital converters use several methods to calculate an output signal that represents the sampled input. The most common method is sigma-delta, but some devices combine delta and successive approximation. Learn more about how ADCs work here.